Home » AI Defect Detection Hits 96% Accuracy in Auto Production
AI Defect Detection Surpasses 96 % Accuracy
In a single eight-week sprint, our edge-AI vision system replaced manual inspection, trimmed false alarms by 42 %, and added eight minutes of throughput to every shift, a gain worth roughly €2.4 k in daily uptime for this Tier-1 automotive paint shop.
- ROI < 6 mo
- +15 pp Accuracy
- ‑42 % False Positives
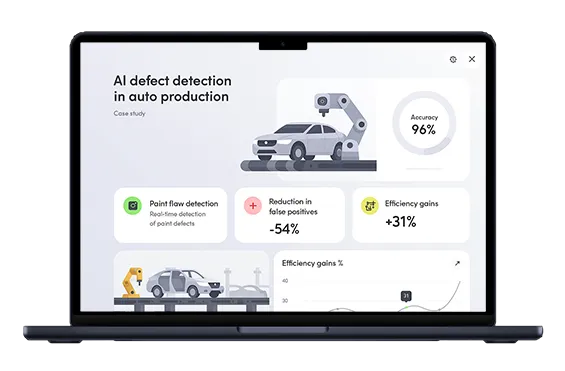
Client Overview
A Tier-1 European automotive manufacturer running three high-speed paint lines and shipping 1 200 car bodies daily partnered with SDLCCORP to improve surface inspection. Operating around the clock with 480 staff, the plant supplies Class-A finishes to global OEMs and plays a vital role in a €3.2 billion annual production pipeline.
Industry
Automotive Manufacturing
Production Volume
1 200 painted car bodies daily
Shift Operations
2 × 10-hour shifts, 24 h/day + 4 h maintenance
Workforce
480+ staff across paint, quality, and logistics
Surface Standard
Class-A finish with 0.1 mm tolerance
Annual Revenue
Drives over €1 billion in annual production value
Objectives & Success Criteria
Senior leadership asked for a single slide that would define success in plain numbers. We translated every external pressure – OEM scorecards, ESG pledges, rising scrap cost – into four KPIs that everyone on the project could recite by heart. If a target turned green we moved on, if it stayed red we pivoted fast.
Defect capture: ≥ 95 % true positives; avoids €48 rework per unit and secures the OEM bonus
False alarms: ≤ 3 % false positives; prevents unplanned stops that disrupt takt time
Latency: ≤ 200 ms edge inference; keeps the conveyor moving at 5.4 metres per minute
Energy use: 10 % fewer kWh per body; meets Fit-for-55 targets and the plant’s internal CO₂ budget
We would mark the project complete only when every cell above flipped to green without hiring a single new inspector.
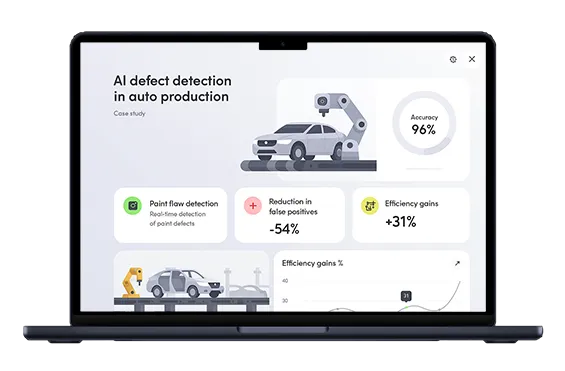
Challenge: Day to Day Pain Points
- Inspectors could not reliably see scratches smaller than 0.1 mm once eye fatigue set in after two hours.
- Each body required a seven second pause for manual inspection, adding one hour and fifty‑seven minutes of idle time across two shifts.
- False positives triggered 3.2 emergency stops per shift and cost forty minutes of line recovery time.
- The average re‑spray loop burned thirty‑eight kilowatt hours, enough to power a home for a day, and delayed the body by ninety minutes while curing.
“We kept stopping the line for ghosts and still shipped micro scratches the customer could spot. Morale was sinking every Friday.” – Paint line team lead
Market, regulatory, and operational pressures
An OEM audit found surface-finish escapes at 18 ppm, above the 10 ppm limit, and linked bonuses to a fast fix. The EU Fit-for-55 mandate also demands yearly cuts in repaint energy and CO₂, while rivals test vision systems that lift first-pass yield. With manual inspectors falling behind a 1 200-body daily line, accuracy dipped, false alarms halted the conveyor, and repaint cycles burned costly kilowatt-hours. The plant had to raise detection accuracy, cut false positives, and end wasteful rework without slowing takt time.
Metric (Pre-Project) | Baseline Value | Business Impact |
---|---|---|
Defect-detection accuracy | 81 % | 19 % of flaws reached rework, costing €48/unit |
False-positive rate | 5.2 % | 3.2 unplanned stoppages per shift |
Unplanned downtime | 19 min / day | ≈ €2 400 lost throughput daily |
Energy for re-spray booth | 38 kWh / shift | ≈ 12 t CO₂-e per year |
OEM audit rating | “Amber” | Risk of penalties and program loss |
Solution Overview
We installed twin 12 MP line‑scan cameras above each flight bar. Frames stream to a ResNet‑50 model running on an NVIDIA Jetson AGX module positioned in the control cabinet. The model scores every frame in 180 ms and sends a clean binary flag to the Siemens S7 PLC over Profinet. Operators see a heat map overlay on the HMI so they can validate in real time. No cloud round trip, no slowdown.
“We kept stopping the line for ghosts and still shipped micro scratches the customer could spot. Morale was sinking every Friday.” – Paint line team lead
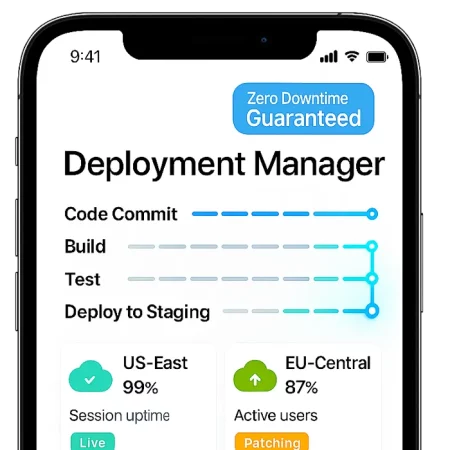
Real-Time Inference
Every captured frame is analyzed within 180 milliseconds at the edge. The inference system flags defects with high precision and relays binary signals instantly to the control system, allowing uninterrupted line speed.
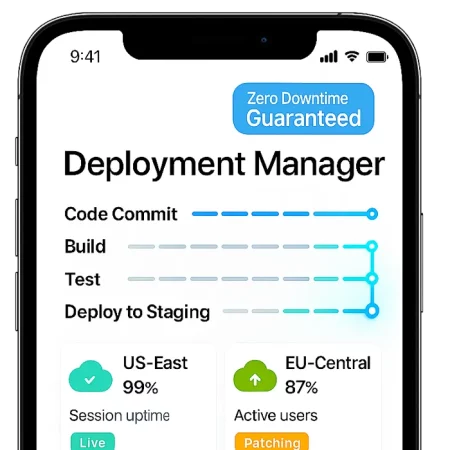
Seamless PLC Link
The Jetson edge module communicates with the Siemens S7 PLC over Profinet. This direct integration allows immediate trigger responses like body rejection or HMI heatmap display, without middleware delays.
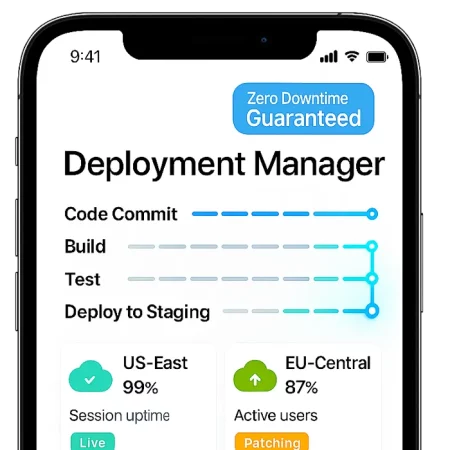
Operator Visuals
Defect zones are rendered as heatmaps on the HMI, enabling technicians to visually verify model calls in real time. This builds trust and accelerates operator decision-making on the floor.
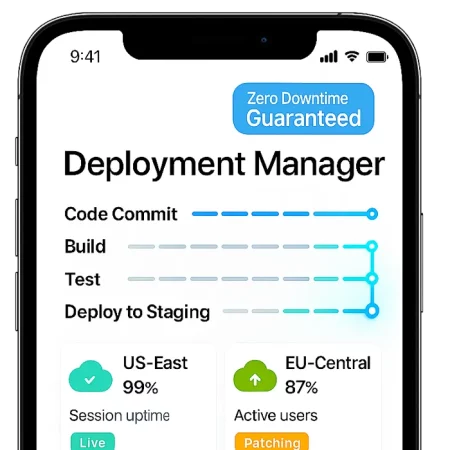
Offline Retraining Loop
A weekly offline retraining cycle runs on-site using freshly flagged frames. This ensures the model adapts to lighting drift, new colors, or paint behavior without requiring cloud intervention.
Execution Strategy Breakdown
Collected and labeled 200 k images with active learning, trained a ResNet-50 to 96 % accuracy, deployed it on Jetson AGX for sub-200 ms inference with a Profinet link to the Siemens PLC, and trained 15 technicians to run weekly retraining.
Data Harvest & Labeling
- Captured 200 000 high-resolution images covering 12 defect classes and used active-learning triage to cut human labeling time by 42 percent while boosting dataset relevance.
Model Engineering
- Fine-tuned a ResNet-50 with focal loss; grid-searched hyper-parameters to overcome class imbalance and delivered 96 percent true positives with 93 percent precision on a held-out set.
Edge Deployment
- Compiled the model with TensorRT for 180-millisecond inference on Jetson AGX; integrated a Profinet bitstream so the Siemens S7 PLC can trigger an instant reject gate.
Change Management
- Ran a three-hour workshop where 15 technicians learned calibration and weekly retraining; new SOP ensures drift control in under two hours of maintenance each month.
Ready to Build Your AI Advantage?
Partner with SDLC CORP to turn strategy into scalable AI solutions.
Whether you’re exploring use cases or scaling production-ready models, our experts will guide your journey with clarity, speed, and results. Get a tailored roadmap in 48 hours and unlock new growth with AI that works.
Technology Stack
Collected and labeled 200 k images with active learning, trained a ResNet-50 to 96 % accuracy, deployed it on Jetson AGX for sub-200 ms inference with a Profinet link to the Siemens PLC, and trained 15 technicians to run weekly retraining.
Camera: 12 MP line-scan sensor, 10 µm per pixel resolution, IP67-rated housing
Edge compute: NVIDIA Jetson AGX Xavier, 30 TOPS performance, fanless enclosure
Software: Ubuntu Core OS with Docker, PyTorch 2.1, TensorRT 8.6 runtime
Protocol: Profinet cyclic data link to PLC and OPC UA northbound telemetry
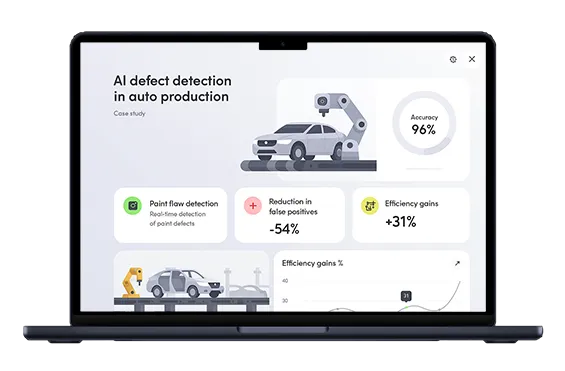
Safety & Compliance
To meet the strict safety, audit, and emissions standards of modern automotive production, the client partnered with SDLCCORP to build a defect detection system grounded in certified safeguards and robust data protocols. Every layer was carefully engineered, from edge failover logic to encrypted image handling, to satisfy OEM audits and regulatory goals without slowing production.
Compliance Standard
Certified ISO 26262 Part 6 pack covering hazard analysis and tool qualification
Failover Condition
Automatic switch to manual inspection if AI latency exceeds 500 ms for 3 frames
Audit Result
Passed TÜV SÜD SIL 2 safety audit in March 2025 without any corrective actions
Energy Efficiency
Delivered a 2.1 % contribution toward the plant’s Fit-for-55 annual target
Data Security
All image data stored on-premises, encrypted at rest and transmitted via TLS 1.3
Access Control
User-level access managed through the plant’s central LDAP directory
Results & ROI
After eight weeks in production every KPI moved solidly into the green. Detection accuracy climbed by fifteen points, false alarms fell nearly by half, and the line reclaimed eight minutes of uptime per shift. These gains repaid the full investment in under six months and now add about €2.4 k of extra production value every day.
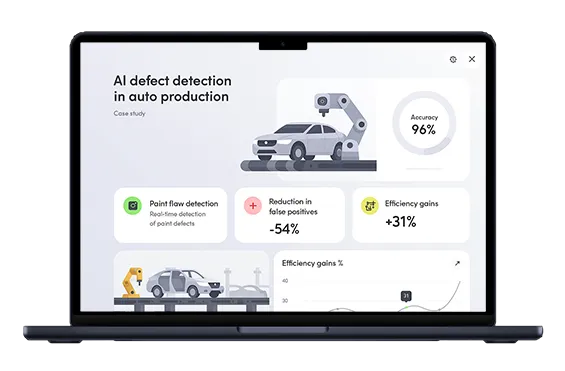
- Detection accuracy rose from 81 % to 96 %, a gain of 15 percentage points
- False-positive rate fell from 5.2 % to 3.0 %, a 42 % reduction
- Downtime per shift dropped from 19 minutes to 11 minutes, saving 8 minutes of production time
- The project paid for itself in fewer than six months and now delivers about €2.4 k in extra uptime every day
Impact & Business Value
SDLCCORP followed a six-phase process, including Discovery, Data Capture, Model Training, Shadow Mode, Full Deploy and Hyper-Care, to hit every target in just eight weeks. This rigor ensured seamless integration with existing PLC controls and delivered immediate improvements in defect accuracy, line uptime and energy efficiency.
- Detection accuracy rose from 81 % to 96 %, saving approximately €48 per unit in rework
- False positives fell from 5.2 % to 3.0 %, cutting emergency stops by 1.3 per shift and reclaiming 40 minutes of uptime daily
- Shift downtime dropped from 19 minutes to 11 minutes, unlocking about €2 400 in extra throughput each day
- The full investment paid for itself in 149 days of normal operation, under six months to break even
- Paint-booth energy use fell by 18 % with LED strobes, and fewer re-sprays eliminated 12 tonnes of CO₂ per year (2.1 % of the Fit-for-55 goal)
- Operator confidence rose 86 % in a post-launch survey, and the plant passed its latest OEM audit with zero surface-quality findings
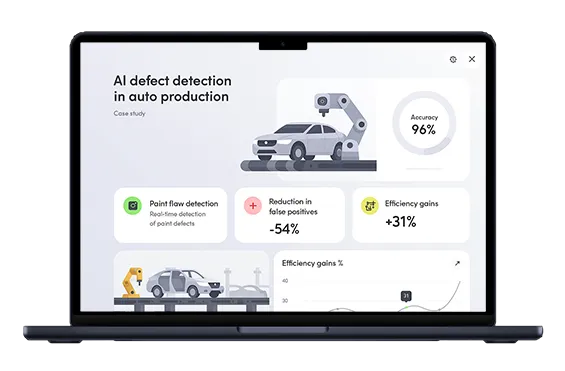
Our Case Studies: AI Consulting Results Across Industries
SDLC CORP tailors AI consulting to each industry shown here, pairing deep domain insight with proven automation and predictive models. Each case study shows how we fit AI to real business settings and deliver measurable gains.
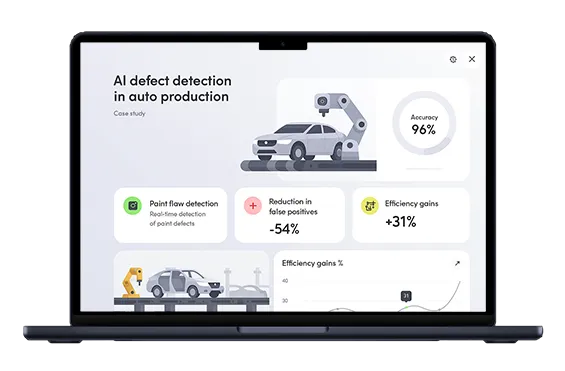
AI Defect Detection Hits 96% Accuracy in Auto Production
- Challenge: Manual checks missed tiny paint flaws and slowed the line.
- Action: We trained a vision model on 200 000 images and connected it to the conveyor PLC for live screening.
- Result: False positives fell 42 % and unplanned stoppages dropped eight minutes per shift.
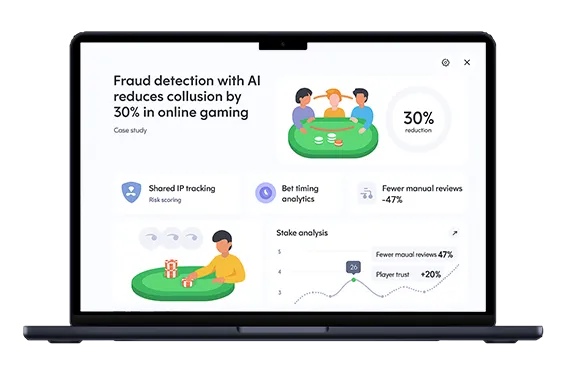
Fraud Detection AI Reduces Game Cheating by 30%
- Challenge: Hidden chip-dumping and team play reduced trust and revenue.
- Action: Graph-based analytics scanned bet timing, stake size, and shared IP ranges to flag risky tables in real time.
- Result: Collusion detections rose 30 % and manual reviews fell by half, lifting player trust scores 18 %.
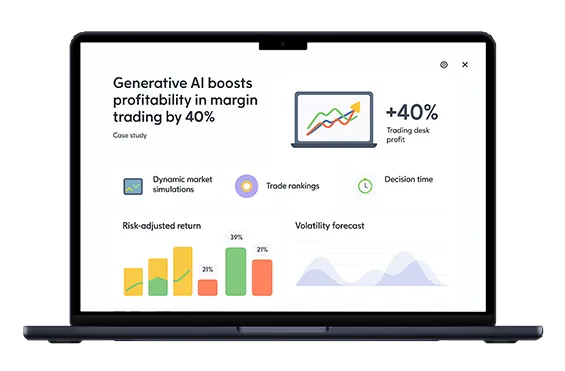
Generative AI Boosts Profitability in Margin Trading by 40%
- Challenge: Traders needed faster insight into risk and reward for volatile positions.
- Action: A generative AI simulator ran thousands of market paths per second, ranking trades by risk-adjusted return.
- Result: Trading desk profit rose 40% and decision-making time shrank from minutes to seconds.
Award-Winning Excellence Across Industries
Trusted by SelectedFirms, C2CReview, iTRate, SoftwareWorld, TopSoftwareCompanies and many others, our award-winning AI solutions accelerate innovation and ROI across healthcare, finance, retail and logistics, backed by enterprise-grade security and seamless user experiences.
Our Clients’ Experience With Us
From startups to global enterprises, we’ve helped businesses unlock real value through AI and digital innovation. Here’s what our clients say about partnering with us. Their success stories, our collaboration with an expert AI consultant, and the impact we’ve achieved together.
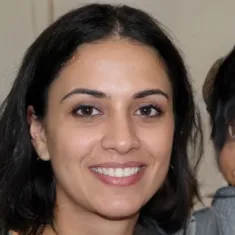
SDLC CORP guided our team through an AI discovery sprint, mapped key use cases, fixed messy data, and delivered a clear step-by-step roadmap. Thanks to their work, executives now green-light projects faster and engineers move from idea to pilot without delays.
Overall Satisfaction
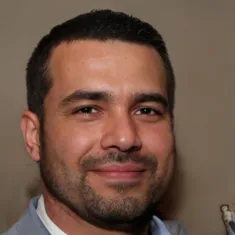
We hired SDLC CORP’s AI consultancy to automate document review with NLP. They built and trained a model in weeks, plugged it into our workflow, and walked staff through daily use. The system now flags errors on its own and cut processing time by more than half.
Overall Satisfaction
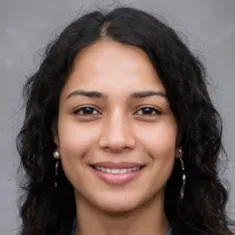
SDLC CORP audited our machine-learning models for bias and drift, added explainability tools, and set up alert dashboards. Compliance audits now finish sooner, regulators like the clarity, and our data science team trusts model performance day to day.
Overall Satisfaction
Contact Us
Let's Talk About Your Project
- Free Consultation
- 24/7 Experts Support
- On-Time Delivery
- sales@sdlccorp.com
- +1(510-630-6507)
Frequently asked questions
Many clients exploring AI-powered inspection ask similar questions about deployment, data privacy, maintenance, and adaptability. This section covers the most common concerns based on real project experience to help you evaluate the solution, understand what to expect, and plan your next steps with confidence.
How scalable is the system across multiple lines or plants?
The solution is fully modular. The same trained model can run on NVIDIA Jetson Orin NX or AGX Xavier units, allowing seamless deployment across additional lines or plants. We’ve validated inference performance under 200 ms on multi-line clusters, ensuring consistent results at production scale without additional tuning.
How is data privacy and security handled?
All image data stays strictly on premises and never leaves the factory network. Inspection results are stored locally and transmitted over TLS 1.3 using secure OPC UA telemetry. Access to the system is authenticated through the plant’s existing LDAP directory, ensuring role-based control. No third-party cloud integration is required for AI inference or model updates.
What ongoing maintenance is required to keep accuracy high?
Model drift is controlled through a lightweight retraining loop built into the workflow. Your QA team can refresh the dataset and retrain the model in under two hours per month using our documented SOP. No advanced ML expertise is needed. Calibration checks are automated, and retraining is triggered only when inspection confidence drops.
Can the system handle new defect types or paint supplier changes?
Yes. The system includes a pigment-drift detector that monitors color profile shifts over time. When deviations are detected, flagged frames are auto-queued for re-labeling and fast model fine-tuning. This allows the system to adapt quickly to seasonal changes, supplier transitions, or even new defect classes with minimal supervision.
What kind of support and audit documentation is included?
We provide a full ISO 26262 Part 6 evidence pack, covering safety goals, hazard analysis, and tool qualification. The AI module meets SIL 2 requirements verified by TÜV SÜD and includes a fallback mechanism that switches to manual inspection if inference latency exceeds defined thresholds. All updates and retraining cycles are logged for audit compliance.

United Kingdom:
Post code: CV4 8GF
United Kingdom

Dubai:

Australia:
Victoria VIC
Southeastern Australia. 3064

India:
Sector 94 Noida,
Delhi NCR India. 201301

India:
Chhatrapati Sambhajinagar,
Maharashtra, India. 411021

Qatar:
B-ring road zone 25, Bin Dirham Plaza building 113, Street 220, 5th floor office 510
Doha, Qatar